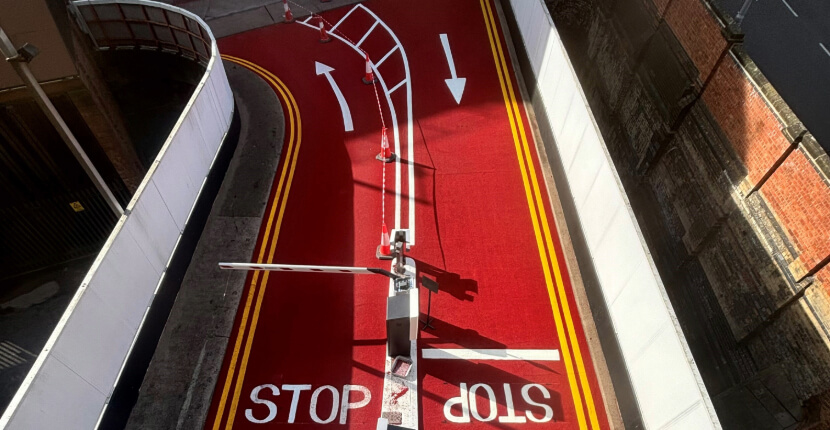
High Friction Surfacing in Heston
Enquire Today For A Free No Obligation Quote
High Friction Surfacing (HFS) is an innovative surface treatment solution designed to enhance skid resistance and improve road safety across various environments, particularly in Heston, where our company specialises in delivering top-tier anti-skid surfacing solutions.
Our expertly installed High Friction Surfacing systems utilise a combination of durable materials, such as epoxy resin and thermoplastic, in conjunction with high-quality aggregates, to ensure unparalleled grip and accident prevention on critical roads, including motorways, pedestrian crossings, and sharp bends.
What are the Benefits of High Friction Surfacing?
High friction surfacing in Heston offers several key benefits for road safety and performance:
Enhanced Skid Resistance
HFS significantly increases the friction between vehicle tyres and the road surface. This improved grip is particularly important in wet or icy conditions, where traditional road surfaces may become slippery and hazardous.
High friction surfacing reduces the risk of vehicles skidding, providing drivers with better control, especially during sharp manoeuvres or emergency braking.
Shorter Braking Distances
One of the most critical safety benefits of HFS is its ability to drastically shorten braking distances. By increasing the friction coefficient, vehicles can stop more quickly, which is crucial in preventing collisions.
This feature is particularly valuable in areas such as pedestrian crossings, school zones, and traffic signal approaches where reaction times are limited.
Increased Safety at Hazardous Sites
HFS is most commonly applied in locations prone to accidents, such as:
- Sharp Bends: Helps vehicles maintain grip while navigating tight curves.
- Steep Gradients: Reduces the risk of vehicles losing control when ascending or descending slopes.
- Roundabouts: Enhances tyre-road interaction for better control at entry and exit points.
- Junctions and Intersections: Provides additional braking assurance for vehicles approaching stop signs or traffic lights.
- Pedestrian Crossings: Reduces risks for vulnerable road users by enhancing vehicle stopping power.
Durability
HFS materials, typically composed of calcined bauxite and specialised binders, are designed to withstand heavy traffic loads and adverse weather conditions.
This durability ensures that the surfacing maintains its high-friction properties for several years, even under demanding use. This longevity reduces the need for frequent repairs or reapplication.
Cost-Effectiveness
While HFS installation may involve higher upfront costs compared to standard surfacing, the long-term benefits outweigh this initial investment. By preventing accidents, it lowers societal costs related to emergency services, medical treatment, insurance claims, and legal expenses.
Additionally, the extended lifespan of the surface minimises ongoing maintenance and repair expenses.
Compliance with Safety Standards
In many countries, road authorities mandate or recommend the use of HFS in high-risk areas to comply with safety regulations.
Installing HFS helps road operators meet these requirements and ensures accountability in reducing accident rates.
Versatility
HFS can be applied to various road types, including asphalt and concrete, making it suitable for urban, rural, and industrial environments.
It is also adaptable to different traffic conditions, from light-use pedestrian zones to heavy motorway applications.
Improved Traffic Flow
By reducing the frequency of accidents, particularly in high-risk areas, HFS contributes to smoother traffic movement.
Fewer incidents mean less congestion, improving overall travel efficiency and reducing delays for road users.
Increased Public Confidence
Drivers, cyclists, and pedestrians feel safer when using roads equipped with HFS, fostering trust in local infrastructure.
This safety perception can encourage greater use of certain routes, reducing bottlenecks on alternative paths.
Environmental Benefits
By preventing accidents, HFS indirectly reduces vehicle idling and traffic congestion, which contributes to lower fuel consumption and emissions.
Moreover, the long lifespan of HFS reduces the frequency of maintenance-related roadworks, which can also mitigate environmental impacts.
High Friction Surfacing Cost in Heston
The average cost of high friction surfacing is Β£40 per m2.
The price of HFS in Heston can vary depending on several factors, such as the type of aggregate used, the size of the area, and local labour costs.
By investing in high-friction surfacing, individuals not only improve road safety but also reduce long-term maintenance costs, making it a wise decision for thoughtful planners.
Where is High Friction Surfacing Installed?
High Friction Surfacing (HFS) is typically installed in locations where enhanced road safety is critical due to increased risks of skidding or accidents. Common installation areas include:
- Sharp Bends and Curves: To prevent vehicles from losing control, especially on tight or sharp corners.
- Pedestrian Crossings: Increases vehicle stopping power near zebra crossings or school zones.
- Approaches to Junctions and Roundabouts: To reduce accidents caused by sudden braking or poor control when approaching intersections.
- Traffic Lights and Stop Sign Approaches: Helps vehicles stop more quickly at controlled intersections.
- Slip Roads and Motorway Exits: Applied where vehicles transition from high-speed to lower-speed zones, reducing skid risks.
- Steep Inclines and Declines: Improves traction on slopes where braking distances increase.
- Blackspots or Accident-Prone Areas: Areas with a high incidence of collisions benefit from HFS to mitigate accident rates.
- Railway Level Crossings: Enhances safety by reducing the likelihood of vehicles skidding when crossing tracks.
HFS is generally used in high-risk areas to improve road safety and reduce skid-related accidents.
How is High Friction Surfacing Installed?
The installation of High Friction Surfacing in Heston involves a specific process to ensure durability and effectiveness. Here are the key steps involved:
- Surface Preparation: The road surface must be clean, dry, and free of any contaminants like oil or debris. Any potholes or cracks are repaired to create a smooth base.
- Application of Binder: A specialised resin or bitumen-based binder is applied to the road surface. This acts as an adhesive for the high-friction aggregate. The binder is usually heated and applied either by machine or hand, depending on the size of the area.
- Spreading the Aggregate: High-friction aggregate, typically calcined bauxite due to its excellent durability and friction properties, is evenly spread over the binder. The aggregate is applied before the binder hardens, ensuring it adheres properly.
- Compaction: The aggregate is pressed into the binder using specialised equipment to ensure good adhesion and uniform coverage.
- Curing: The binder is left to cure, typically for several hours, depending on the material and weather conditions. During this time, traffic is usually diverted or managed to avoid disturbing the surface.
- Sweeping and Inspection: Once the binder has cured, any loose aggregate is swept away. The surface is inspected to ensure even coverage and adherence.
- Opening to Traffic: After the curing process is complete and the surface has been swept, the road is reopened to traffic.
This process ensures that the high-friction surface provides maximum grip and durability. Proper installation is key to the long-term effectiveness of HFS.
What Materials are Used for High Friction Surfacing?
High Friction Surfacing in Greater London utilises a variety of materials including epoxy resin, aggregate, thermoplastic, and binders to create a durable surface treatment that significantly enhances skid resistance and road safety.
The selection process for these materials is crucial, as each component plays a vital role in achieving optimal performance under various conditions.
Epoxy resin offers impressive bonding strength and resistance to wear, ensuring long-lasting adhesion to the pavement.
The choice of aggregate is equally significant; various types such as crushed stones or hardened granules are carefully evaluated for their size and texture to maximise skid resistance and durability.
This is often guided by rigorous testing protocols to determine the most suitable options for specific environments.
Thermoplastic materials are often selected for their ease of application and adaptability to different temperatures.
Binders serve to increase the flexibility and longevity of the surface, further contributing to its overall durability.
By meticulously analysing these elements, the efficacy of HFS can be significantly enhanced, ultimately leading to safer driving experiences.
What is High Friction Surfacing?
High Friction Surfacing (HFS) is a specialised surface treatment designed to enhance skid resistance on roads, providing a crucial layer of safety that prevents accidents, especially in high-risk areas.
High Friction Surfacing in TW5 0 involves applying a durable, high-grip material to road surfaces, which significantly improves traction under various weather conditions. This treatment is particularly effective on sharp bends, intersection approaches, and steep gradients where the risk of skidding is heightened.
By fortifying these vulnerable spots, roads are made much safer for drivers, cyclists, and pedestrians alike.
The integration of this innovative surfacing solution has been proven to lower accident rates and enhance public confidence in road safety.
Get In Touch
If youβre interested in learning more about High Friction Surfacing (HFS) in Heston and how our services can enhance road safety, we encourage you to get in touch with us for enquiries and consultations.
Our dedicated team is ready to provide you with personalised information regarding the numerous benefits of HFS, including its ability to significantly reduce accidents due to improved traction.
Whether youβre overseeing a municipal project or simply want to enhance the safety of your local roads, we can tailor our solutions to meet your needs.
Frequently Asked Questions
What is a High Friction Surface?
A high friction surface refers to a specialised road treatment designed to significantly increase the skid resistance of a pavement.
What is High Friction Surfacing Material?
High Friction Surfacing (HFS) material refers to the combination of a durable binder and high-performance aggregate used to create a high-traction road surface.
When to Use High Friction Surfacing?
High Friction Surfacing (HFS) should be used in areas where road safety is critical, particularly where the risk of skidding or accidents is higher.
What Types of Surfaces can High Friction Surfacing be Applied to?
High Friction Surfacing (HFS) can be applied to a variety of surfaces including asphalt, bitumen, and concrete, making it a versatile solution for enhancing skid resistance and road adhesion across different road types, especially in high wear zones.
What are the Safety Standards for High Friction Surfacing?
Safety standards for High Friction Surfacing in Heston are crucial in ensuring that installations meet regulatory requirements for skid resistance, accident prevention, and overall road safety.
To achieve optimal results, understanding the specific guidelines outlined by organisations such as the Department for Transport is essential. These regulations often mandate rigorous testing procedures to assess surface texture, friction levels, and road adhesion.
Regular audits and maintenance are key components to maintain compliance and enhance performance over time.
Adherence to these standards not only promotes safe driving conditions but also minimises accident risks and enhances traffic safety.
HFS must be applied in accordance with best practices for installation, which encompass factors like weather conditions, surface treatment, and road markings.
Engaging qualified contractors who are knowledgeable in these regulations is crucial for achieving desirable outcomes.
By prioritising these safety measures, communities can effectively prevent accidents and enhance overall road safety.
How does High Friction Surfacing Improve Road Safety?
High Friction Surfacing in Heston significantly improves road safety by enhancing skid resistance, which is critical for preventing accidents, especially in high-wear zones and during adverse weather conditions.
When we consider how HFS operates, it becomes clear that its unique texture plays a pivotal role in increasing tyre grip. This is particularly vital when vehicles navigate sharp bends or junctions, where loss of control can often lead to serious accidents.
The application of HFS in regions prone to rainfall has demonstrated remarkable effectiveness.
What Regulations Must be Followed for High Friction Surfacing?
When installing High Friction Surfacing in Heston, it is essential to comply with various regulations and safety standards to ensure the effectiveness and safety of the surface treatment.
These regulations play a crucial role in enabling safer driving conditions, particularly in areas prone to accidents due to low traction.
An HFS installation not in line with such criteria can lead to serious implications, including increased accident rates and potential legal ramifications for stakeholders involved.
Adhering to compliance ensures not only the longevity of the surface but also the safety of all road users.
Key regulations include local and national safety standards, material specifications, and installation procedures.
Regular inspections and maintenance schedules must be followed to uphold compliance and performance.
Failure to adhere to these can result in costly reworks and compromised safety outcomes.
Ultimately, the importance of following these regulations cannot be overstated, as they collectively contribute to the overall safety and reliability of HFS installations.
How does High Friction Surfacing Differ from Traditional Road Surfaces?
High Friction Surfacing differs from traditional road surfaces because it uses a combination of aggregates, resins, and binders to create a rougher surface texture that increases friction between tyres and the road.
This differs from traditional road surfaces, which are typically smoother and can become slippery when wet.
How Long does it Take to Install High Friction Surfacing?
The installation time for High Friction Surfacing on an average-sized area, such as a pedestrian crossing or small road section, usually takes 1 day to install. Bigger projects, such as a stretch of road or car park can take up to a week.
The install time of HFS can vary depending on the size and complexity of the project. Our experienced team can complete installations in a timely and efficient manner, minimising disruption to traffic and road users.
Is High Friction Surfacing Suitable for All Types of Roads?
High Friction Surfacing is suitable for a wide range of road surfaces, including motorways, roundabouts, junctions, bridges, and even airport runways.
It is particularly effective in high wear zones and sharp bends. It is also suitable for both urban and rural areas and can be applied to both new and existing road surfaces.
Find More Info
Make sure you contact us today for a number of great high friction surfacing services in London.
Here are some towns we cover near Heston TW5 0
Hounslow, Southall, Hayes, Hanwell, HillingdonFor more information on high friction surfacing in Heston TW5 0, fill in the contact form below to receive a free quote today.
β β β β β
High Friction Surfacing provided outstanding service from start to finish. Their expertise in installing high friction, anti-skid surfaces has made a significant difference in road safety in our area. The team was professional, and the installation was seamless. We’ve seen a noticeable reduction in accidents, especially in wet conditions, thanks to the improved grip. Highly recommend their services for anyone looking to enhance road safety!
Danielle Holland
Greater London
β β β β β
We are incredibly pleased with the work done by High Friction Surfacing. The high friction, anti-skid surface they installed on our site has dramatically improved vehicle control, especially on bends and heavy traffic areas. Their attention to detail and commitment to quality is second to none. The project was completed on time and with minimal disruption. I would definitely use their services again!
Tom Garrex
Greater London